Lithium Battery Requirements For Cathode Materials In Terms Of Battery Performance.
- Share
- Issue Time
- Jun 27,2019
Summary
The main components of lithium-ion batteries are positive electrode, negative electrode, electrolyte, diaphragm, etc. The storage and release of lithium ion energy is realized by the redox reaction of electrode materials.
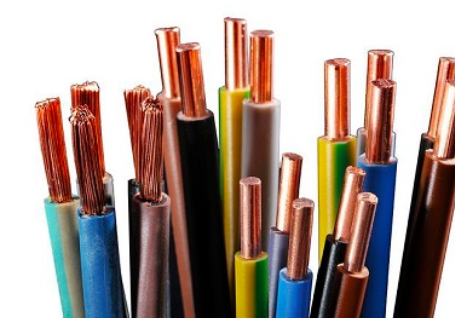
1 Introduction: Lithium battery cathode material
The main components of lithium-ion batteries are positive electrode, negative electrode, electrolyte, diaphragm, etc. The storage and release of lithium ion energy is realized by the redox reaction of electrode materials. The positive active material is the most critical core material of lithium ion battery.
In the research of cathode materials for lithium-ion batteries, Professor GOODENOUGH, the American scholar "the father of lithium batteries" made a great contribution: during the inauguration of the University of Oxford in the United Kingdom in 1980, it was discovered that lithium cobalt oxide (LiCoO2, LCO for short) can be used as a positive electrode for lithium batteries. The following year, he mentioned the feasibility of lithium nickelate (LiNiO2, also known as LNO) as a positive electrode material in the LCO patent; in 1983, the first attempt was made to use lithium manganate (LiMn2O4, LMO for short) as a positive electrode material for lithium ion batteries; In 1997, he developed the olivine structure cathode material - LiFePO4 (LFP). In addition, in order to solve the problem of unstable lithium nickelate performance, Professor DAHN of Canada and Professor Xiao Yan of Japan conducted a lot of doping modification research. In 1997, Toda Company of Japan took the lead in applying for the earliest lithium nickel cobalt aluminate (LiNi1). -x-yCoxAlyO2, referred to as NCA) patent; in 1999, Liu Zhaolin and Yu Aishui of the University of Singapore introduced Mn modification on the basis of lithium nickel cobaltate. The first nickel-cobalt-manganate (LiNi1-x-yCoxMnyO2, namely three Metamaterial, NCM).
After nearly three decades of rapid development, based on the research results of the above scientists, lithium cobaltate, lithium manganate, lithium nickel cobaltate (LiNi1-xCoxO2, also known as NC), lithium nickel cobalt manganese oxide, lithium nickel cobalt aluminate, Cathode materials such as lithium iron phosphate have been industrialized and expanded into many fields. With the demand for high energy density cathode materials for new energy vehicles, lithium nickel cobalt manganese ternary materials have become the most important and the largest cathode materials (Figure 1). In the past 20 years, domestically produced cathode materials have gone abroad, and some products are in the world's leading position. Some advanced battery materials companies such as Dangsheng Technology, Tianjin Bamo, Hunan Ruixiang, and Mengguoli have emerged.
2 Lithium battery cathode material product standard technical specifications
2.1 Lithium-ion battery requirements for cathode materials
The positive electrode is the core component of the battery, and its advantages and disadvantages directly affect the battery performance. In general, the following requirements are imposed on the positive active material:
·Allow a large amount of Li+ to be embedded and released (larger specific capacity);
·Has a high oxidation-reduction potential (high voltage);
·The embedding has good reversibility and small structural change (long cycle life);
·High lithium ion diffusion coefficient and electronic conductivity (low temperature, good rate characteristics);
·High chemical/thermal stability, good compatibility with electrolyte (good safety);
·Rich in resources, environmentally friendly, and cheap (low cost, environmentally friendly).
In general, the key performance indicators of the cathode material are: chemical composition, crystal structure, particle size distribution, tap density, specific surface area, pH value, initial discharge specific capacity, first charge and discharge efficiency, cycle life, and the like.
2.2 The main element content of the cathode material
The positive electrode materials in lithium ion batteries are all lithium-containing oxides. Generally, the higher the lithium content, the higher the capacity. For example, lithium manganate has a Li content of only 4.2%, while lithium cobaltate and lithium nickelate reach about 7.1%, and lithium-rich manganese-based can be as high as about 10%. If the material composition is fixed, the main element content should be given in the form of the actual test mean plus tolerance to achieve the corresponding electrochemical activity and maintain stability between batches. The positive electrode materials in lithium ion batteries are all lithium-containing oxides. Generally, the higher the lithium content, the higher the capacity. For example, the lithium content of lithium manganate is only 4.2%, while the lithium cobaltate and lithium nickelate reach about 7.1%, and the lithium-rich manganese-based one is as high as about 10%. If the material composition is fixed, the main element content should be given in the form of the actual test mean plus tolerance to achieve the corresponding electrochemical activity and maintain stability between batches.
2.3 Crystal structure of the cathode material
The crystal structure of the positive electrode material of lithium ion battery is mainly divided into three categories: α-NaFeO2 layered type, olivine type, and spinel type. In the positive electrode material, the pure phase of LiCoO2 is relatively easy to prepare, and the product has an α-NaFeO2 layered structure, corresponding to the 50-0653# card issued by the Joint Committee on Power Diffraction Standards (JCPDS); LiMn2O4 Pure phase is easier to obtain, the product has a spinel cubic structure, corresponding to JCPDS 5-0782# card; LiFePO4 has a Fe +2 price and must be prepared in an inert atmosphere. The product has an olivine structure corresponding to JCPDS 83- 2092# card.
2.4 Particle size distribution of cathode material
The particle size of the positive electrode material directly affects the preparation of the battery slurry and the pole piece. Generally, the large particle size material slurry has low viscosity and good fluidity, and can be used with less solvent and high solid content.
The particle size of the positive electrode material is usually measured by a laser particle size analyzer, and the equivalent diameter D50 of the largest particle when the cumulative distribution in the particle size distribution curve is 50% is regarded as the average particle diameter. The particle size and distribution of the cathode material are closely related to the precursor, sintering, and crushing processes, and should normally exhibit a normal distribution. Lithium cobaltate is generally prepared by using cobalt trioxide and lithium carbonate as raw materials. The sintering characteristics are very good, and it can be grown by controlling key factors such as Li/Co, sintering temperature and heating rate, so that the raw material requirements are low. The powdered material which grows by sintering and cracking tends to have large irregular particles, which are prone to scratches and broken bands during pulp coating and coating. Therefore, the lithium cobaltate standard is used for the equivalent diameter Dmax of the largest particles in the particle size distribution curve. The limit.
Most of the lithium manganate uses the same raw material as the alkaline manganese battery, electrolytic manganese dioxide (EMD). The production process is to deposit a whole piece of MnO2 plate by electrolytic process, and then obtain it by peeling and crushing. The raw material itself has large shaped particles, so the lithium manganate standard also limits Dmax. The Dmax of the dynamic lithium manganate is small, mainly considering the factor of using the spherical manganese source precursor, and the particle size distribution is controllable. In the industrialization of materials such as lithium nickel cobaltate, lithium nickel cobalt manganese oxide, and nickel cobalt cobalt aluminate, chemical coprecipitation is usually used to achieve atomic level mixing of elements such as Ni, Co, Mn, and Al, and high by controlling crystallization. density. Therefore, the particle size distribution of such materials is narrower than that of lithium cobaltate. The requirements of D10 and D90 are proposed in the standard, and K90 can be further calculated as an index reflecting the narrow distribution of particle size.
(1)
The size design of the D50 is also considered for different applications. The rate-type material is usually small in D50 to shorten the distance of Li+ in the solid phase diffusion inside the positive electrode particles. High-pressure solid materials usually have a large D50, and most of them use the Bimodal method, so that small particles are sufficiently interstitial between large particles to achieve the closest packing effect.
2.5 Density of cathode material
The volumetric energy density of a lithium ion battery is highly dependent on the density of the active material. The density of the positive electrode material is closely related to the atomic weight of the elements, crystal arrangement, crystallinity, sphericity, particle size and distribution, density, etc., and is affected by the preparation process. The density of the positive electrode material is divided into bulk density, tap density, powder compaction density, pole piece compaction density, theoretical density, and the like.
The bulk density is usually measured by the Scote volume meter method: the powder flows freely into the cloth box through the screen, and alternately passes through four glass plates with a tilt angle of 25°, and the funnel is free to fall down the measuring cup at a certain height, from the net weight of the powder. The volume of the measuring cup is calculated.
The tap density is obtained by adding a certain weight of powder to a graduated transparent measuring device, and measuring the weight of the unit volume powder after a predetermined number or time of vibration of a certain amplitude and frequency under prescribed conditions.
Powder compaction density is the addition of a certain weight of powder to a hard mold having a fixed diameter and height. Under pressure, the powder moves and deforms to form a compact having a certain density and strength. The results were calculated from the net weight and compression volume of the powder.
The compact density of the pole piece is made by mixing the material with a small amount of binder and conductive agent, coating, drying and rolling into a positive electrode sheet, compaction density = area density × (pole piece rolling thickness collecting body × body thickness). After rolling at different pressures, the value corresponding to the critical state in which the folded pole piece does not appear to be transmitted is the ultimate compaction density.
The oretical density is an ideal crystal that assumes that the material does not have any macroscopic and microscopic defects. The cell constant is obtained by XRD to determine the cell volume, which is used to remove the total mass of all atoms in a single unit cell. The tap density test method is simple and is an important indicator for measuring the active material of the positive electrode.
The the oretical density of LCO reaches 5.06g/cm3, followed by NCM, NCA, LMO, OLO, and LFP is the lowest, only 3.57g/cm3. It is not difficult to see that lithium cobalt oxide has the highest density, which is also an important reason why it cannot be replaced by other materials in the smartphone market. The same material used in the rate type battery has a large drop in corresponding tap density and compaction density due to the use of a small particle solution. Lithium iron phosphate has the lowest theoretical density and the smallest D50. The tap density and the compact density of the pole pieces are all in the bottom of several common cathode materials.
2.6 specific surface area of the cathode material
When the specific surface area of the positive electrode is large, the rate characteristic of the battery is good, but it is generally easier to react with the electrolyte, which deteriorates circulation and storage. The specific surface area of the positive electrode material is closely related to particle size and distribution, surface porosity, surface coating and the like. In the lithium cobalt oxide system, the small particle size type product has the largest specific surface area. Lithium iron phosphate is poorly conductive, the particles are designed in the form of nano-aggregates, and the surface is coated with amorphous carbon, resulting in the highest specific surface area among all positive electrode materials. Compared with the cobalt system, the manganese-based material has a characteristic that it is difficult to be sintered, and its specific surface area is also large overall.
2.7 Residual alkali content of cathode material
When preparing the cathode material, a slight excess of Li/Me is generally used to ensure complete lithiation of the material from the inside to the outside. Therefore, most of the surface of the positive electrode material will leave a certain amount of excess lithium, which is mostly in the form of Li2CO3. For nickel materials such as NC, NCM, and NCA, the higher the Ni content, the more the material mixing and the more the residual alkali amount; the more serious the battery slurry viscosity and the worse the battery storage performance. The residual alkali test is usually carried out by acid-base potentiometric titration or manual titration, and the positive electrode powder is dispersed into a certain amount of pure water, filtered, and a certain volume of the filtrate is measured and titrated with a standard hydrochloric acid solution. Phenolphthalein and methyl orange were selected as indicators, and two equivalence points appeared in the vicinity of pH ≈8 and pH ≈4, respectively, and the volume of standard hydrochloric acid used was recorded separately. However, for materials such as NC, NCM, and NCA, the test process should be extra careful. Because high-nickel materials are mostly in the form of agglomerated particles, Li-Me is prone to appear in the process of dispersing in water, and continuous lithium deposition occurs. The process of sample preparation and testing should be fine, accurate and controllable. Even so, Li2CO3 mainly reflects the surface Li, and LiOH is the sum of Li on the particle surface, Li in the grain boundary, and Li in the 3a position in the surface crystal structure.
2.8 moisture content of the cathode material
The moisture content of the positive electrode material is closely related to its specific surface area, particle size and distribution, surface porosity, surface coating, and the like. The moisture content has a great influence on the battery pulping. Usually, the positive electrode slurry mostly uses polyvinylidene fluoride (PVDF) as a binder, and N-methylpyrrolidone (NMP) as a solvent. In this organic system, the large molecular weight PVDF is not completely dissolved, but exists in the form of a sol. When the moisture and residual alkali of the positive electrode material are high, the organosol system is destroyed, and PVDF will be precipitated from the NMP, causing the slurry to have a sharp increase in viscosity and even a jelly phenomenon. Lithium iron phosphate has a large specific surface area and easy to absorb air moisture because its primary particles are nanoparticles. Therefore, a wide range of moisture content is given, but most of them are controlled below 300 ppm, otherwise jelly is easily formed during battery pulping.
2.9 Impurity content of cathode material
In addition to the intentionally introduced doping element, the lower the impurity element of the positive electrode material, the better. Impurity elements are generally introduced through raw materials and production processes and need to be controlled at the source. The most common impurity elements are Na, Ca, Fe, Cu, and Na is high in both the precursor and the lithium salt, and Ca is mainly introduced by the lithium salt. Lithium iron phosphate itself is Fe and most of the precursors are soluble salt materials such as sulfates and chlorides, which are easily incorporated into the crystal during the precipitation process. Therefore, these standards strengthen the control requirements for SO3-2 and Cl-.
The safety issue of lithium-ion batteries has always been a focus of attention. It has been found that metal foreign bodies directly introduced from equipment or environmental pollution in the manufacturing process of batteries and their materials are easy to pierce the diaphragm, causing the battery to explode. Most of the common equipment is made of stainless steel, galvanized steel, etc., and some of them can be collected by magnetic separation. Therefore, the relevant standards of three materials such as LCO, NCA, and OLO have proposed control of magnetic foreign matter (mainly metal elements such as Fe, Cr, Ni, and Zn), and it is required to reach 300 ppb (1 ppb = 1 × 10-9 μg / g). )the following.
2.10 Specific capacity of the cathode material, first efficiency, voltage platform requirements
The electrochemical properties of the specific capacity, initial charge and discharge efficiency and voltage platform of the positive electrode material are closely related to the main element content, crystal structure, particle size, charge and discharge voltage, charge and discharge current. The basic rule is that the higher the Li content, the larger the specific capacity. Objectively speaking, the platform capacity ratio emphasizes the discharge voltage platform. The various positive electrode materials vary greatly. It is better to change to the average voltage or the median voltage, which is more effective for ensuring and improving the energy density of the battery.
2.11 Rate characteristics of the cathode material
Lithium-ion batteries used in e-cigarettes, power tools, RC airplanes, drones, and automotive start-up power supplies have high requirements on battery and material rate performance, and are required to achieve 5C, 10C, or even 30C charge and discharge. The rate characteristic of the positive electrode material is related to factors such as particle size, crystallinity, Co content, and C coating amount. High-rate lithium cobaltate can achieve 10C discharge, and the ratio of 10C/1C reaches over 90%.
2.12 Cycle life of cathode material
Lithium-ion batteries for electric vehicles are expected to achieve a cycle life of more than 2,000 cycles. Electric vehicles are generally used for short-term use. If you charge the electric meter for 2 days, the cycle life of 2000 times can support the pure electric vehicle on the road for nearly 11 years. If Tesla's Modal S carries 60 kW·h of electricity and lasts for 390km, it will be used for 50km per day, and will be charged once every week. The cycle life of 1000 times can meet its 19-year age. The function of the smart phone is getting stronger and stronger. In addition to the basic functions of the phone and SMS of the ordinary mobile phone, the existing functions of taking photos, surfing the Internet, WeChat, online shopping, office, games, etc., the display is getting bigger and bigger, the body is more The thinner the lighter, the higher the energy density of the battery is, and the cycle life is more than 500 times to support the mobile phone for more than 2 years. The cycle life of the positive electrode material is related to its crystal structure, charge and discharge depth, and preparation process. The lithium iron phosphate material has a stable olivine structure, and theoretically allows lithium in the structure to be completely removed, and the charge and discharge reversibility is good, so that excellent cycle performance is exhibited. Under the actual road conditions, the lithium-ion battery for vehicles will be affected by the battery itself and the environment, and the temperature will rise above 50 °C. Therefore, it is also necessary to pay attention to high-temperature cycle and high-temperature storage performance. Lithium manganate is prone to Jahn-Teller effect under high temperature conditions, causing Mn dissolution and crystal structure collapse.
3. Conclusion
The existing positive electrode materials are all processed in a large-scale industrial application after being processed into a practical battery and satisfying the above requirements in terms of comprehensive performance. In the preparation process, the positive electrode material will fluctuate due to changes in human, machine, material, method, environment, test and other conditions. Therefore, from the raw material procurement-production-transport-sales and other aspects, standardization operations must be carried out in accordance with the specifications. And in accordance with the relevant standards (below: Table 1) to verify, to ensure the product's practicality, consistency and reliability. This requires key performance indicators for products, semi-finished products, raw materials, etc., which must be determined by setting standards.